
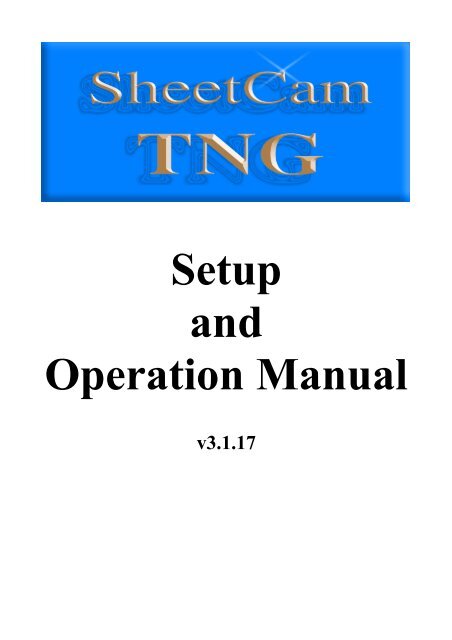
Remove JP-382C board from enclosure by unscrewing two screws at the bottom side of control box and two screws at the back panel:Ĥ. Locate JP-382C board and disconnect connectors of cable sets for X, Y and Z axis motor outputs, power supply and E-Stop switch. Take your control box and remove all screws of the top cover:Ģ. G-code M54 P1 enables THC, M54 P0 disables it.ġ.
#Sheetcam direction arrow size software
PlanetCNC TNG software uses dedicated g-code to enable and disable THC device. This should be set by testing, try finding value that suits your machine. Maximal height compensation value oppose to relative Z0. Minimal height compensation value oppose to relative Z0. This pin will receive compensation signal for axis movement in positive direction. This pin will receive compensation signal for axis movement in negative direction. Select Machine axis that would perform THC compensation moves. Parameters related to THC are located in: File/Settings/Control/THC THC device sends control signals to motion controller which then dynamically compensates Z axis and thus maintains constant cutting height. So based on the voltage value we can maintain constant height of plasma torch above the material. Bigger the distance between the plasma torch and material higher the voltage and vice versa.

Heat emitted from plasma could deform workpiece material, usually metal sheet, in such case plasma cutter would not cut at constant height which could result as a faulty workpiece or could damage plasma cutter in the process. SheetCAM software offers wide range of plasma toolpath options and it is very user friendly.
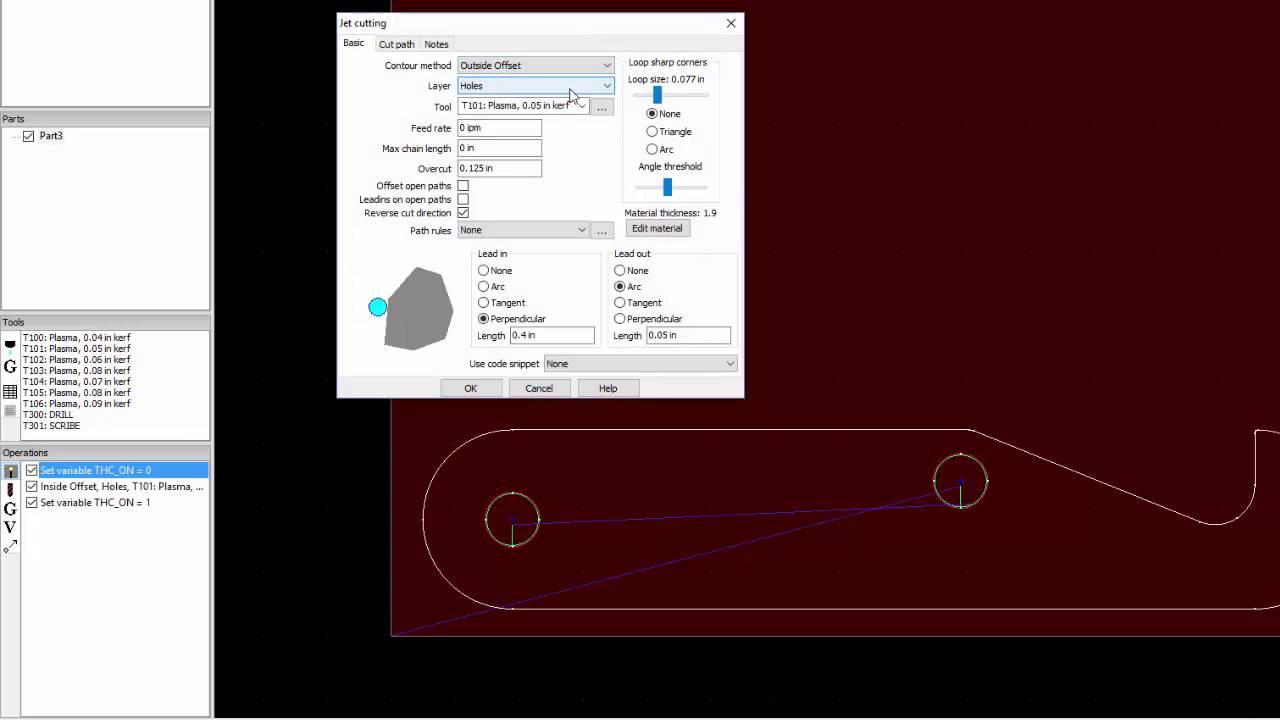
You can use special CAM software intended exclusively for plasma cutting. User should also pay attention to ignition delays, pierce heights etc. For this purpose toolpath should include lead in and lead out moves. So your work-piece could be well off from specified dimensions. The reason for this is when plasma ignites and arc pierces trough material, this leaves a mark on material. Special approach should be considered when designing toolpath program for plasma CNC machines. Plasma cutters itself sometimes do not satisfy standards of electromagnetic compatibility (EMC), so make sure that your plasma cutter is within EMC regulations. External power supply for motion controller is very recommended. So special care should be taken into account when wiring machine electronics.īe sure to use shielded cables for motors, limit switches. Plasma cutter is a great source of electromagnetic interference. Ethernet protocol is more robust than USB and therefore more suitable for industrious environments. Machine should be properly designed for such type of machining, considering slag, steel dust, high temperatures, moisture, grease etc.įor plasma CNC machine we recommend using Mk3 controller for its Ethernet support. Like any other type of CNC machine, plasma machine has it own specifics. It’s used mostly for cutting Steel, aluminium and other conductive materials. Plasma CNC cutting machine is one of the most commonly used types of CNC machine.
